In March, Chris Warden and Catherine McBain travelled to Boston, MA for the 4th edition of the Preserving the Recent Past Conference. This conference unites North American conservation specialists to address key issues in the preservation of Modern historic resources. With Modern places now beyond 50 years of age, they remain significant for their innovation in postwar materials and techniques for suburban and urban landscapes. Buildings and sites from this era showcase the dynamism, creativity, and societal tensions, reflecting mass suburbanization, urban changes, Modern styles, innovative products, and social movements.
The conference was held at the Boston Architectural College in Back Bay—home to a plethora of modern and post-modern buildings. Many of the conference field sessions, workshops and presentations were on buildings within the M.I.T. and Harvard Campuses. Chris and Catherine presented their findings on the work completed to date conserving the architectural aggregate precast concrete at the Lester B. Pearson Building in Ottawa. TRACE has been involved in this project since 2017 serving as the Heritage Architects within the team lead by Dialog Design. Contained below is a brief summary of the material they presented.
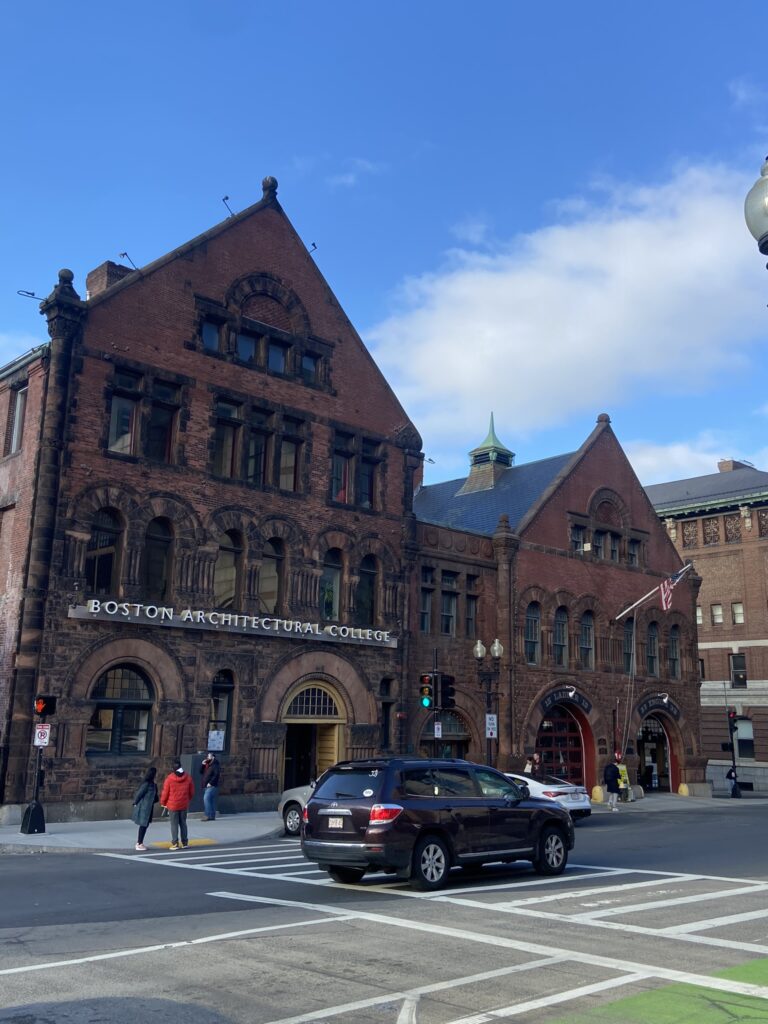
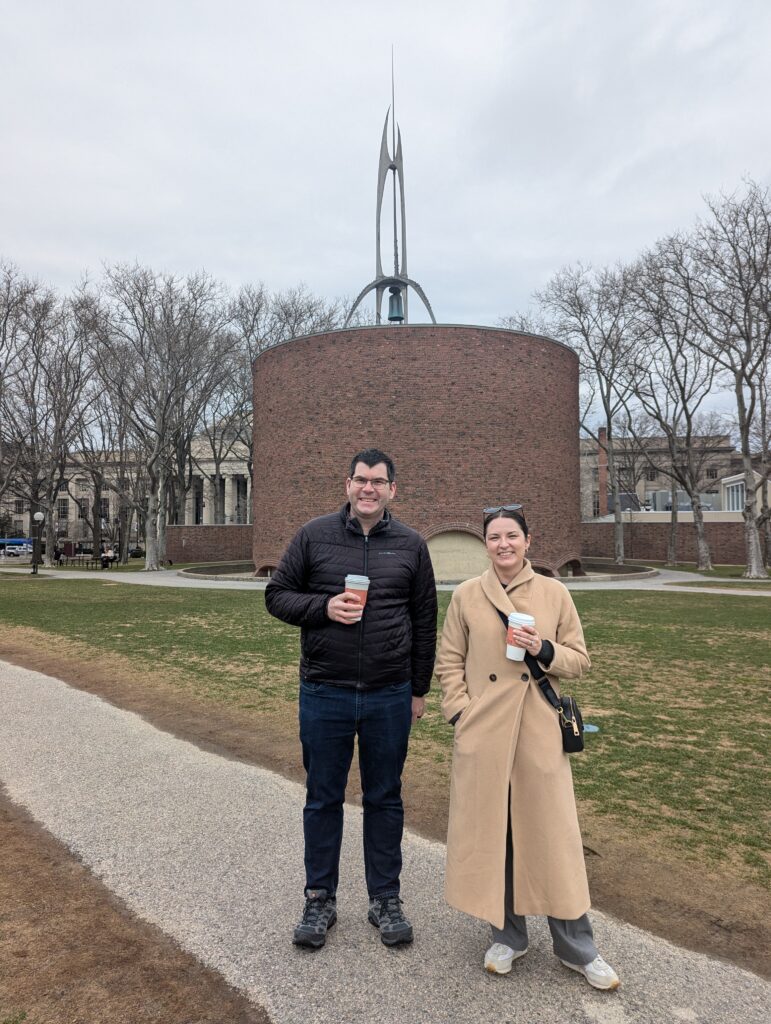
Their presentation reviewed the Lester B. Pearson building (LBPB) including history, materials, and heritage value. They presented their initial strategies, discussed challenges and selected revised methods of concrete repairs. Completed in 1974 and designed by Webb Zerafa Menkes (now WZMH), the same firm that designed the CN Tower in Toronto, LBPB was designated as a classified heritage building in 2012.
The complex is located on Ottawa’s ceremonial route on Sussex Drive, home to many important government buildings and embassies. It was recognized for its strong architectural expression, effective interior layout, superior materials, details, and craftsmanship. The building’s bold sculptural qualities, asymmetrical massing, and use of concrete walls and a monolithic podium anchor it in the landscape.
The building features high-quality, well-crafted materials, including aggregate-faced architectural precast concrete used for exterior cladding and finishes at terraces, bronze-tinted ribbon windows, and bronze hardware and interior details. The goal of the concrete repairs and much of the building’s renovation investment was to extend the building’s lifecycle by another 50 years.
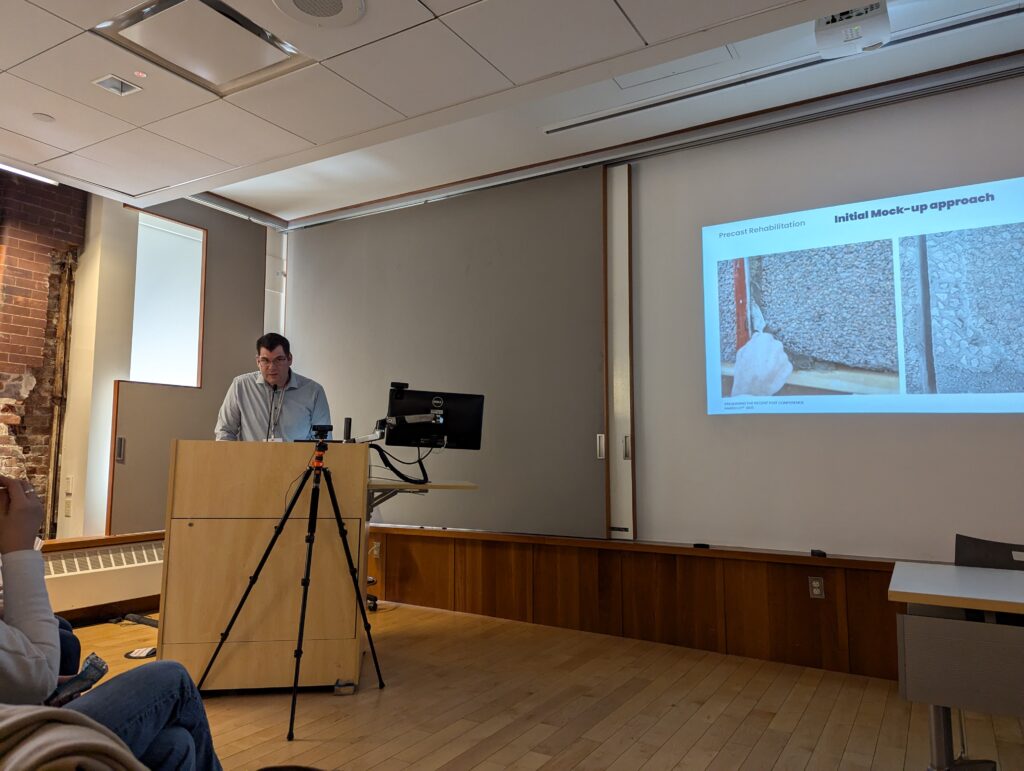
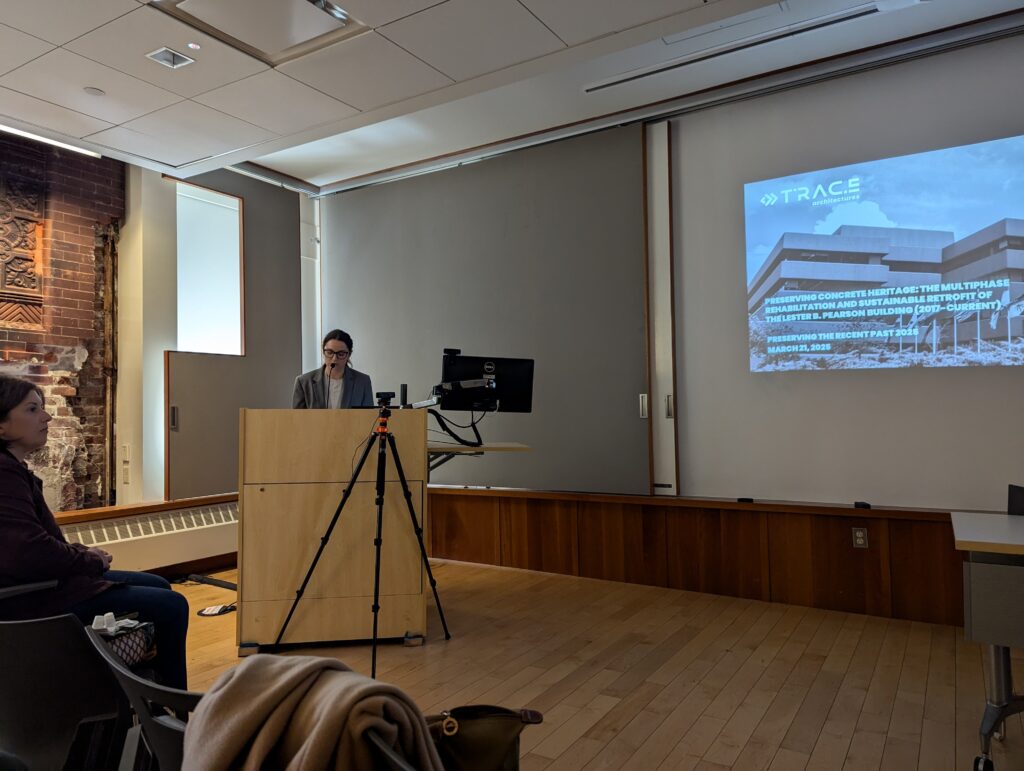
The precast concrete cladding, approximately 4 inches thick with an aggregate granite finish, was the focus of the rehabilitation treatment program. Various deterioration types were observed, including spalling, cracking, improper previous repairs, and biological growth. Early stages of construction involved mock-ups to test rehabilitation treatments for precast concrete. Spall treatments included applying restoration mortar with aggregate set into it. Challenges included the lack of workability of repair mortar and difficulty in achieving consistent aggregate distribution.
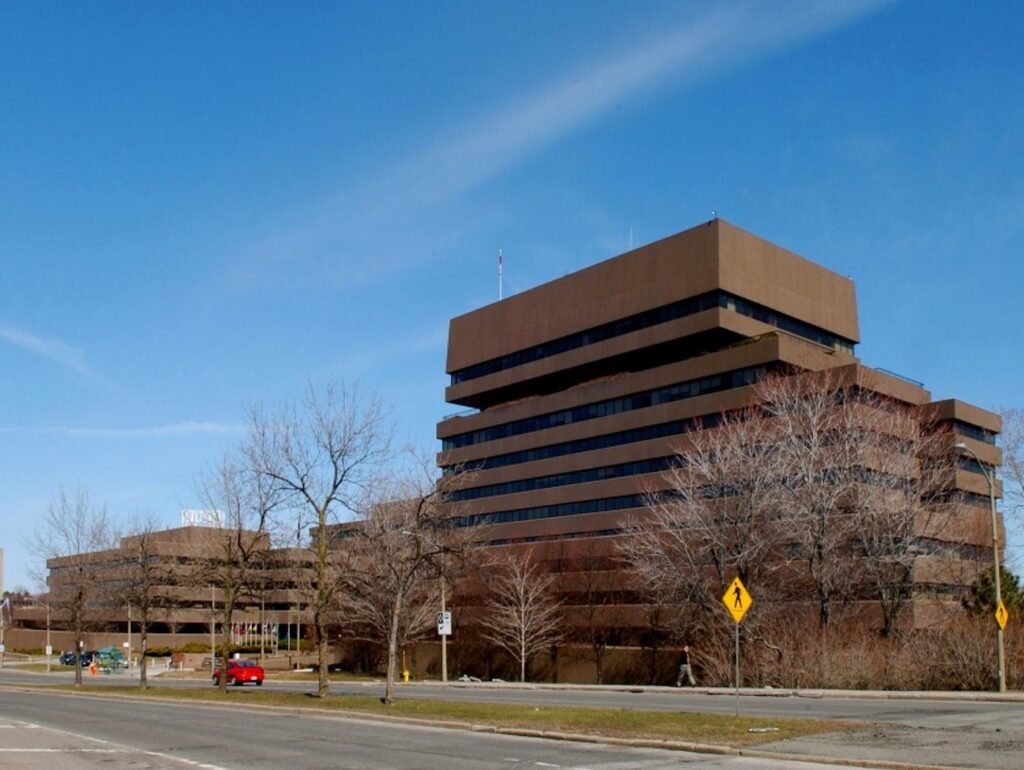
The revised approach involved removing and cleaning the spall, roughening the base surface, and building up the patch in layers. A layer of tinted epoxy adhesive was added to accept the aggregate pieces, which were then sanded down to align with the surrounding area. For large spalls, precast concrete Dutchmans were used.
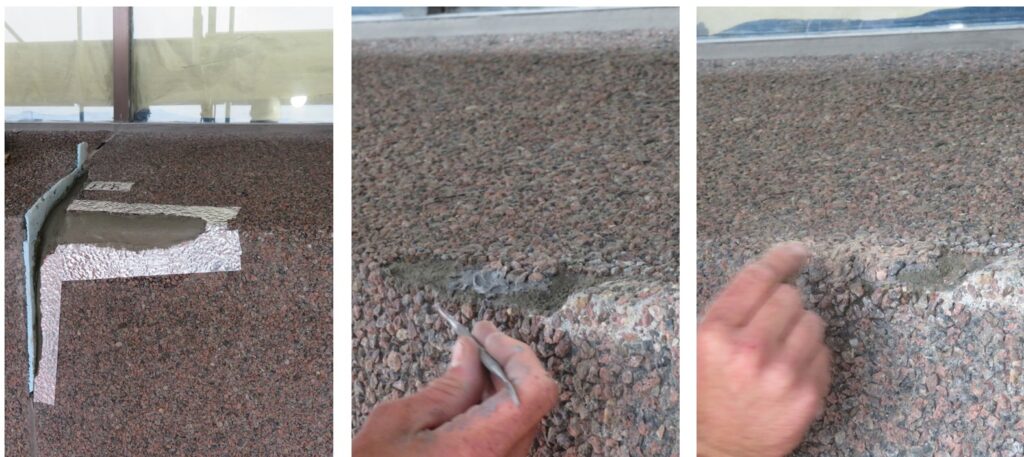
Despite improvements, challenges remained with the visual performance of the finished repair. The mock-up approach allowed the team to work through technical challenges and achieve a high benchmark for the finished product. By the end of the second phase, a good approach to spall repairs was established, ranging from small patches to full panel height repairs.
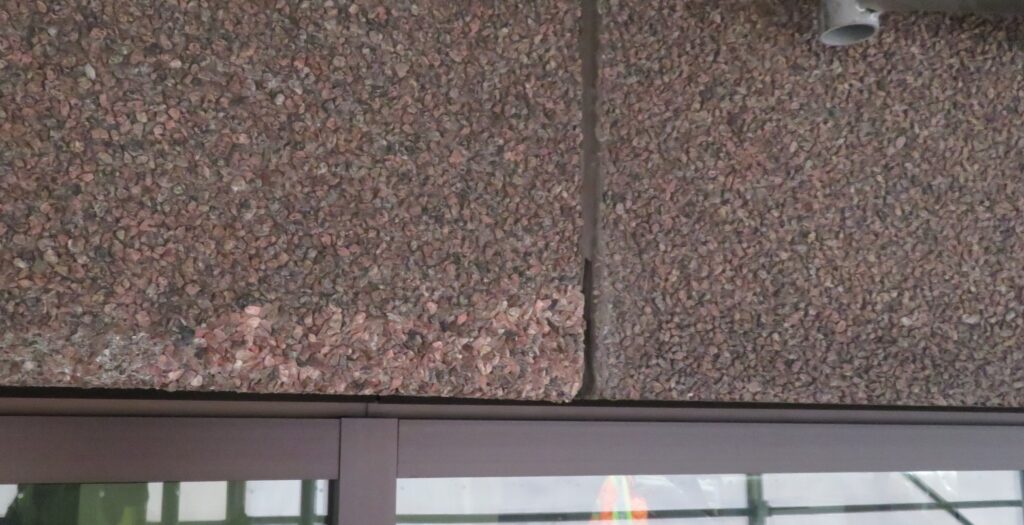
After nearly eight years on this project, the team has learned that addressing deterioration in manufactured products is challenging. Solutions need to be developed for specific materials and environmental considerations. Employing a two-stage approach for spall repairs allowed for greater control over placing aggregate pieces. Cleaning and removing soiling from the exterior precast helped restore the shimmering qualities of the aggregate-faced panels.
The team recognizes the rare opportunity of this type of project, which allowed for significant latitude for inconspicuous experimentation through mock-ups. This was especially valuable in this multi-phase project, building on a lessons-learned approach as the project progressed.